Understanding Hydraulic System Issues in Farm Equipment
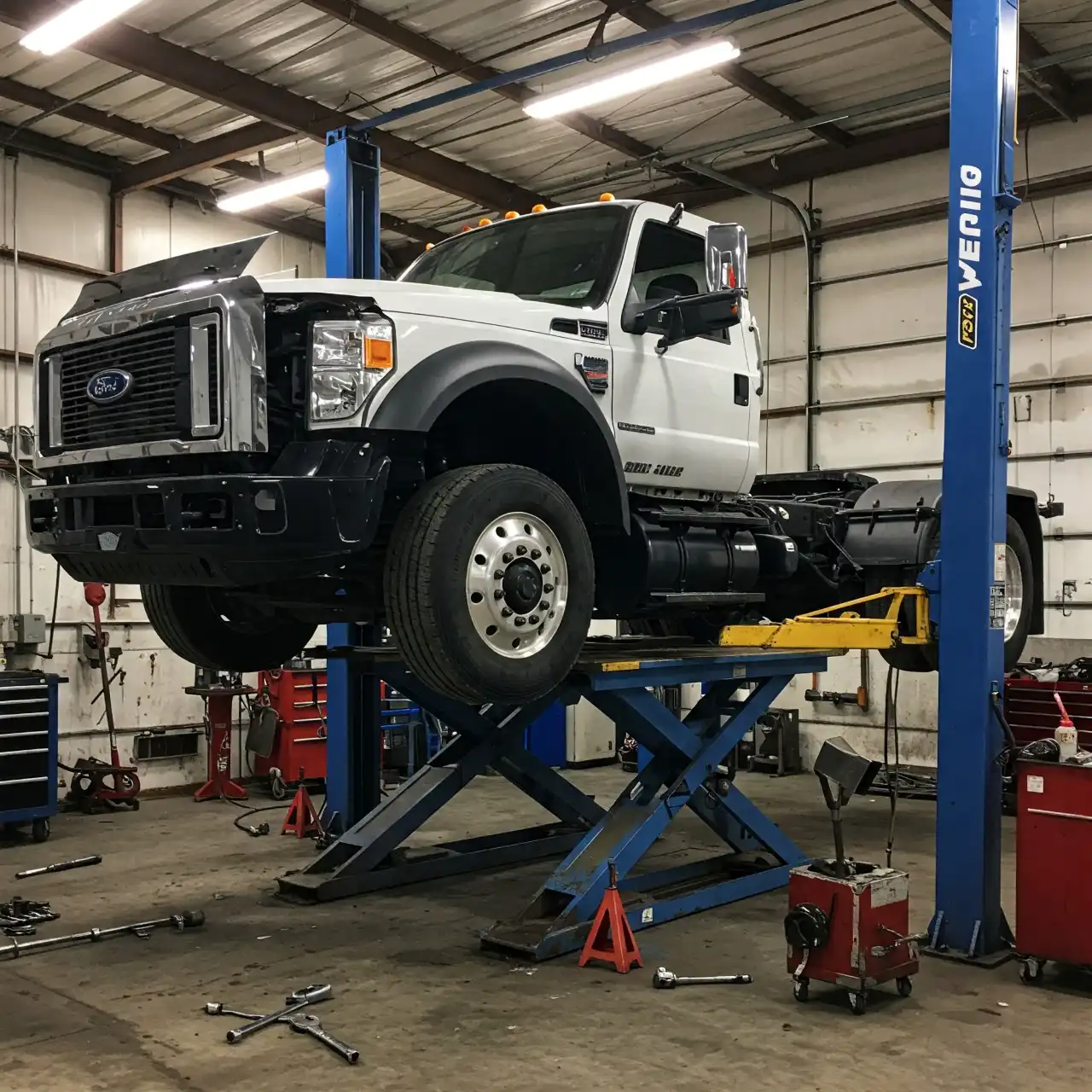
Hydraulic systems are the muscle behind nearly every modern piece of farm equipment. Whether you're lifting heavy loads with a front-end loader, operating booms on a sprayer, or managing multiple implement movements on a baler or combine, hydraulic pressure makes it all possible. However, with power comes vulnerability, and when hydraulics fail, your productivity can come to a halt.
In this guide, we will break down how these systems work, the most common issues farmers face with them, and how to keep your equipment running smoothly during the most critical times of year.
How Hydraulics Power Agricultural Equipment
Hydraulic systems use incompressible fluid to transfer force from one point to another. In agricultural equipment, that force enables smooth, precise, and powerful motion that mechanical systems cannot match. Some common hydraulic functions in farm machinery include:
- Lifting and lowering attachments
- Steering in large tractors or sprayers
- Extending/retracting booms or arms
- Controlling harvesting components (augers, headers)
- Powering loaders, backhoes, and tillage equipment
Key Hydraulic Components
To understand how and why things go wrong, you need to know what makes up a hydraulic system:
- Hydraulic Pump – Creates the flow of pressurized fluid
- Hydraulic Fluid – Transfers force and lubricates components
- Control Valves – Direct the fluid to specific actuators
- Cylinders/Motors – Convert fluid pressure into movement
- Hoses and Fittings – Carry fluid between components
- Reservoir – Stores and cools the fluid
- Filters – Remove debris and contamination
5 Most Common Hydraulic Problems in Farm Equipment
Despite their rugged design, hydraulic systems are sensitive to contamination, heat, and wear. Below are the most frequently encountered issues in agricultural environments.
1. Hydraulic Fluid Leaks
Leaks are the most visible and persistent problem farmers face. High-pressure lines, seals, and connections can break down due to vibration, age, or physical damage. Likely causes:
- Cracked or pinched hoses
- Loose or corroded fittings
- Worn cylinder seals
- Overpressured system components
Symptoms:
- Visible oil pooling on the ground or equipment
- Low fluid levels in the reservoir
- Loss of hydraulic power
- Drifting or sagging implements
What to do: Check all lines and fittings during pre- and post-use inspections. Replace seals proactively and ensure hoses are routed appropriately to avoid abrasion or pinching.
2. Weak or Sluggish Hydraulics
If your attachments are moving slower than usual or struggle under load, you're likely facing a flow or pressure issue. Causes may include:
- Low hydraulic fluid levels
- Clogged filters or screens
- Air trapped in the lines (aeration)
- Failing hydraulic pump
- Worn internal seals in control valves or cylinders
Solution: Start with a fluid level check. If low, inspect for leaks and top up as needed. Bleed the system to release trapped air and replace any clogged filters. If the problem persists, a pump flow test may be required.
3. Overheating Hydraulic Fluid
Excessive heat is a silent killer for hydraulic systems. Over time, heat degrades fluid viscosity and damages seals, leading to wear and decreased system performance. Common causes of overheating:
- Using incorrect or contaminated fluid
- Dirty coolers or radiators
- Worn or misaligned pump components
- Restricted return lines
- Operating under excessive load or duty cycles
Symptoms:
- Burnt-smelling or discoloured fluid
- Reduced responsiveness
- Erratic or inconsistent movement
- Warning lights (on equipment with monitoring systems)
Preventive Tips: Clean cooling elements often, and monitor fluid temperatures during peak operating hours. Use a fluid that meets the manufacturer’s specifications for viscosity.
4. Cavitation and Noisy Operation
Cavitation occurs when air bubbles form and collapse in the hydraulic fluid, causing mini-explosions inside your pump. Left unchecked, cavitation will erode pump surfaces and internal seals. Causes include:
- Low reservoir levels
- Collapsed suction hose
- Clogged intake screen or filter
- Leaking suction line drawing in air
Identifying cavitation:
- High-pitched whining or knocking noise near the pump
- Foamy or milky-looking hydraulic fluid
- Vibration in lines or controls
Fix: Stop operation immediately and inspect the system for air leaks or restrictions. Replace suspect hoses or clean screens as needed.
5. Jerky or Erratic Implement Movement
Jerky or hesitant movement is a clear indication that something in the system is not functioning smoothly. This could be due to:
- Contaminated or degraded hydraulic fluid
- Partially blocked valves or lines
- Internal wear on control valves or cylinders
- Water contamination from condensation
Symptoms:
- Sudden stops or jumps during movement
- Difficulty controlling the speed or position of implements
- Inconsistent flow or pressure at the outlet
Solution: Drain and flush the system if the fluid is contaminated, and test the valve response. Keeping water out of your fluid system is crucial—store your equipment indoors whenever possible, and change the fluid on schedule.
Preventive Maintenance Tips for Farm Hydraulics
Farmers rely on uptime. A failed hydraulic system during harvest or planting can result in thousands of dollars in costs. Preventive maintenance is your best insurance policy.
1. Regular Fluid Checks
- Inspect the fluid level before and after each use.
- Watch for signs of milky fluid (water) or dark, burnt-smelling oil
- Only use the fluid specified by the equipment manufacturer.
2. Replace Filters Consistently
Filters catch particles that would otherwise damage pumps and valves. A clogged filter increases system pressure and strain.
- Replace filters every 250 to 500 operating hours
- More frequently in dusty, wet, or muddy environments
3. Inspect Hoses and Fittings
Walk around your machine and check:
- Hose routing and protection from rubbing
- Fitting tightness and corrosion
- Wet spots or oil sheen around seals
Pro tip: Use UV hydraulic leak detection dye to identify slow leaks.
4. Train Your Operators
Often, the first sign of failure is how a machine feels. Teach farmhands to report anything unusual—like hesitation, noise, or reduced lifting power.
Mobile Hydraulic Repair: Keeping Your Farm in Motion
At IBEX Diesel Repair in Rigby, ID, we understand the importance of every hour during planting and harvest. That’s why we offer mobile hydraulic diagnostics and repairs—saving you the hassle of hauling equipment off-site. Our team is equipped to:
- Pressure test pumps and cylinders
- Replace seals, hoses, and valves onsite
- Diagnose erratic behaviour and overheating
- Top off, flush, and bleed hydraulic systems
When time matters, on-farm service is more than a convenience—it’s a necessity.
Conclusion
Hydraulic systems are essential to modern farming, powering a wide range of equipment, including loaders and harvesters. Unfortunately, they're also one of the most common sources of downtime. By understanding how they work—and recognizing the symptoms of failure—you can reduce the chance of costly repairs and keep your operation running smoothly.
Whether you're dealing with leaks, cavitation, overheating, or low power, staying ahead with routine maintenance and prompt service is key.
And when the problem is too complex or urgent, trust a mobile repair team like IBEX Diesel Repair in Rigby, ID, to get you back in the field, fast.